The Capacity Challenge - Shifting Paradigms in Biopharma Facility Development
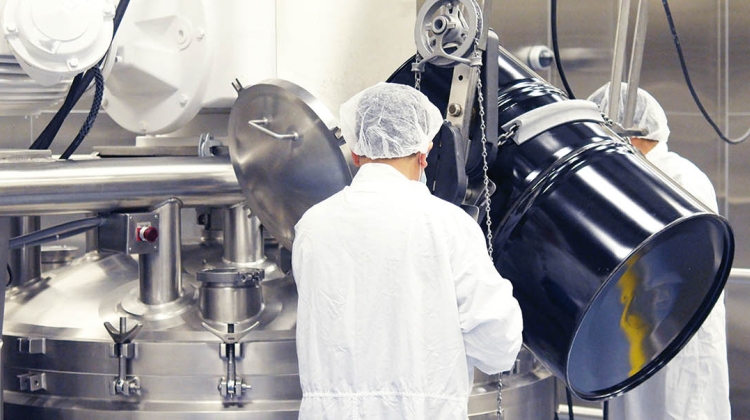
If you have been following the biopharmaceutical industry over the past 20 to 30 years, you were no stranger to discussions about its then-projected rise. In fact, in the mid-1990s and early 2000s, we saw promising growth waves. There was a surge of interest in 2007 and 2008 that ended with the Great Recession; at that time, many in the industry wondered if we would ever see additional large capital investments in biopharma facilities. Cell culture titers were rising, increasing the capacity of existing plants, and interest was shifting to more personalized medicine focused on smaller, single-use strategies.
That has all changed: A new wave of high-volume oncology- and Alzheimer-related therapies, along with the commercialization of low-volume products—including gene and cell therapy—is reinvigorating the industry.
It goes without saying these are very exciting times for life sciences, with a laser focus on “Facilities of the Future” for biopharmaceutical development and manufacturing. These include traditional stainless steel large-scale biomanufacturing facilities and small-volume highly flexible facilities built around single-use technology.
At the 2016 ISPE Biopharmaceutical Manufacturing Conference in San Francisco, California, US, former ISPE Board Chair and Global Pharmaceutical Manufacturing Leadership Forum Chair Andrew Skibo, Head of Global Biologics Operations and Engineering for MedImmune/AstraZeneca, highlighted 10 to 15 megaprojects (those in excess of $350 million) that are in various stages of development, design, and construction. We were very involved with companies, including Regeneron, Bristol-Myers Squibb, and Biogen, as they invested in this new phase of development, for both large- and small-scale manufacturing plants.
We then saw a second wave of investment start last year for both conventional stainless steel and single-use facilities. At that time, a third wave of similar facilities was anticipated, and while the focus has shifted somewhat from large-capital stainless steel projects to large- or mid-capital single-use facilities, 2018’s pipeline still looks strong.
Track progress using key performance indicators, then watch and trust the numbers
Below I outline some of the experiences we’ve had on these projects, in particular how the post–Great Recession market has shifted our paradigms and influenced our goals and execution strategies.
In 2014, the market was alive again but many of the old paradigms were gone—as were key human capital and supply chain elements. We saw a step change in demand, with the potential to stretch engineering, procurement, construction, and qualification capacity across the board. Additionally, there was a renewed focus on delivery from clients, particularly with regard to schedule and return on investment.
Edward Merrow, Founder and President of Independent Project Analysis, Inc., and author of Industrial Megaprojects: Concepts, Strategies, and Practices for Success, issued a fascinating study concluding that for a range of reasons—many of them regarding front-end planning in project definition—approximately 65% of all megaprojects fail to meet business objectives. This is an unacceptable outcome in today’s life sciences industry. Even if processes and capacities are not well defined, we’ve learned and adapted during the past two decades and now have the ability to calculate how to deliver projects to stricter cost and schedule targets in today’s overheated market. We've deployed a new initiative to address these challenges identifying some of the warning signs, and how to respond.
Along with the focus on delivery, end users want to optimize their life cycle costs and minimize time to market. Here are the key themes we see:
- Minimize deployment time: We got used to fast-track projects in the mid-2000s; now we have to talk about “flash-track” or hypercompressed schedules. Our execution strategies must be nimble, and we must manage risk dynamically.
- Simplify the whole design and equipment cycle: replication and standardization are critical.
- Pick the best team: Know your vendors and contractors, and don’t be afraid to collaborate. Depending on geography, a one-stop shop may not be the best answer.
- Know your key players: At the end of the day people make this all happen; secure your team early, because if you don’t, someone else will.
Let’s take each of these in turn:
FLASH-TRACK SCHEDULES
Our internal database shows that before the recent wave of work, the average cycle time for conventional large-scale stainless steel projects was 42 months; now, we are looking to reduce that by 6 to 12 months. How?
- Eliminate the classic critical path: Bioreactors used to be the key, but now if you clone them they can be there as soon as the building is ready. The next step is vendor data; again, if we clone and standardize, we already have that, so the issued-for-construction design can drive forward. Finally: automation, clone, and standardize.
- Embrace hypercompression: We have an extensive overlap in all phases that can be pushed even further by leveraging off-site fabrication for structural modules and super skids. We can also look at using existing buildings to make things go even faster.
- Manage the risk: All this compression pushes our current systems and procedures to the maximum. If we have a robust resource-loaded level-three schedule, we can manage risk and understand “what-if” scenarios. The critical path may not be what we think and may change rapidly. Also, this compression, along with earlier required dates for on-site equipment delivery, drives cash flow forward, so the de facto sanction now occurs at the end-of-concept and not at the front-end design stage—by then you have committed to most of the big stuff.
SIMPLIFYING THE DESIGN
How do we use cloning and replication to simplify design?
- Don't let “good” be the enemy of “good enough.” Design the plant to be operable, then make improvements as production ramps up.
- We spend so much time chasing our tails in design, trying to keep up with development, when the big lesson is we never really get there. Let’s accept that and find a way to get it done rather than make it perfect.
- Maximize replication, use standard off-the-shelf designs for bespoke equipment, and keep decision-makers to a minimum.
- Understand where the design risks are. They’re usually downstream, so fence that in and don’t let it derail the balance of the project.
- Minimize change. Draw a line in the sand at the end of the basis of design process and don’t allow change unless you have a safety or compliance issue or the design simply doesn’t work.
- Bring vendors and contractors in early to streamline design and optimize the packages.
- Track progress using key performance indicators (KPIs), then watch and trust the numbers. If KPIs are off track and design is not going to plan, cost and schedule control will be lost quickly. A classic example is piping and instrumentation diagram changes made after the issued for-design phase: If the changes are increasing, you are not cloning!
CAPACITY AND RESOURCES
Capacity and resources are the final piece to this puzzle.
- Don’t wait until the project kicks off to align and tie in your key suppliers. There simply isn’t room in the flash-track schedule. Bring them in early and allow procurement to do their important work, then drive forward.
- Assemble the best team possible and set the project vision, goals, and accountability metrics. Partnerships and integration are critical, especially in certain geographical locations.
- Remember the people. Many great talents have retired or left the industry, and those that remain are being pushed as hard as possible to work faster. Create a vision and a mission for the project, monitor your organizational health (turnover, burnout, and overtime) and take action to continuously improve. Recognize the staff challenge and try to work smarter.
So where does this leave us? If we remember the following, we are up for the task:
- Set a clear vision.
- Remain disciplined, focused, aligned, and pragmatic.
- Minimize change.
- Take care of your people and celebrate the wins.
Never forget: In the end, it’s about making people’s lives better, and creating a greater tomorrow, which makes it all worth the challenge before us.