An Introduction to Predictive Maintenance

Much has been published on advantages of predictive maintenance, yet many do not realize that it is a tool to help achieve their facility's goals and objectives. If you need to convince management of the need for PredM, this article contains information that you can use as an "elevator speech."
Predictive maintenance (PredM) is a general method that uses ongoing analysis of operational data to determine when equipment maintenance will be required. When applied appropriately, it can reduce maintenance expenses while improving reliability. This article outlines several PredM applications and discusses its applicability to aging facilities.
What is PredM?
Maintenance of GMP facilities is necessary to ensure that they operate in a qualified and validated state and are fit for their intended use. Traditional preventive maintenance has direct costs, may require downtime of equipment or entire production lines, and may increase the risk of contamination. Insufficient maintenance, on the other hand, can cause inefficient operation, premature equipment failure, and other more serious consequences.
Preventive maintenance scheduling is often driven by elapsed time of use (e.g., equipment run hours) or calendar time, with maintenance intervals based on a statistical analysis of past performance and failures. Preventive maintenance can be effective, but it is not sufficient to prevent unplanned downtime through unpredicted failure; it can also result in unnecessary maintenance.
PredM, in contrast, uses ongoing measurements and metrics to calculate equipment health and the corresponding risk of failure. Its primary goal is to predict the need for maintenance, allowing it to be scheduled at convenient times. Other potential benefits include:
- Reduced maintenance cost
- Maintenance is performed when needed, reducing or eliminating the need for regularly scheduled maintenance
- Root cause analysis of problems using performance data enables more efficient repairs and improves the first-time successful repair rate
- Lower frequency of failures
- Less unplanned downtime
- Reduced quality risk
- Opportunity to improve planning, personnel scheduling, and parts availability as unnecessary activities are eliminated.
Unlike traditional scheduled preventive maintenance, which is an intermittent activity, PredM is an ongoing process that involves:
- Data collection and analysis
- Root cause analysis of any identified problems
- Scheduling of maintenance activities as required
PredM uses ongoing measurements and metrics to calculate equipment health and the corresponding risk of failure
Scheduled preventive maintenance continues to remain a viable option, however, because facilities regularly experience shutdowns for product changeovers or vacation breaks. PredM can complement preventive maintenance in these and other circumstances, providing important benefits such as minimizing unplanned downtime, while preventive maintenance can plan for major equipment rebuilds or replacement during shutdown periods.
Calibration Program
PredM relies on data, which must be appropriate for its intended purpose. One way to obtain reliable data on facility and equipment performance is to establish a robust calibration program that identifies the instruments and controls that require calibration—including the frequency, range, accuracy, and precision of those instruments. In GMP facilities, instruments and controls that produce data needed for GMP purposes also become part of the calibration program. Remaining instruments are usually not calibrated, except for the calibration provided by the vendor when first installed.
A robust PredM calibration program should identify and appropriately calibrate those instruments and controls that monitor facility and equipment performance. We emphasize “appropriately” because calibration requirements for frequency, accuracy, and precision will likely be less stringent than those for GMP instruments (often referred to as “GMP critical”). This may mean that more instruments are included in the calibration program than would be the case with preventive maintenance. It may also result in increased costs, but if the information contributes to the PredM program, it will be a value-added proposition.
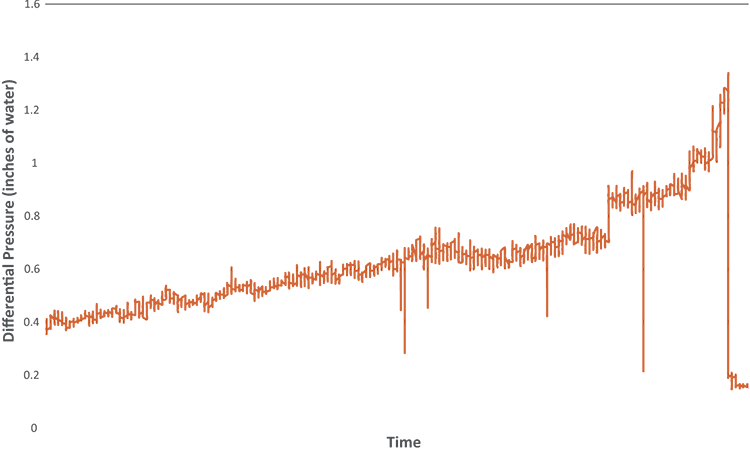
Data Management
Companies in our industry accumulate a tremendous amount of data, so one step may be to manage that data more appropriately. For instance, operations accumulates data on steam sterilizer operation; could some of that data be identified for maintenance as well? Where there is no data source, installing new tools such as vibration or temperature sensors could help anticipate pump failure by adding specific readings to checklists and having maintenance technicians replace items when a certain value or pressure drop is registered.
If data collection and basic data analysis are largely automated, subject matter experts (SMEs) can focus on high-value-added tasks where the consequences will have a large impact—such as HVAC that supports a sterile production facility. In this era of “big data” analytics, specialized software is increasingly used to detect emerging problems and is becoming part of root cause analysis. While it’s important to note that automated tools used to trend and analyze data for GMP decision-making must be validated, automation can result in more consistent application of analysis methods and more timely results.
PredM Examples
The following examples show how PredM could be implemented in pharmaceutical facilities. It is easy to imagine other situations in which the general principles of PredM could be applied.
WFI systems
Water for injection (WFI) system data is customarily acquired and trended by the quality unit. Such monitoring takes data and trends it to determine if the system is operating acceptably and whether the performance is consistent. As mentioned earlier, it is important to integrate information: Does the quality unit include total organic carbon data in its trending reports? Could it provide information on seasonal changes influenced by changes in the water source (surface or well water)? The results of such analyses would be used to make decisions about if/when/how to perform maintenance on the WFI system, and whether engineering changes are needed to ensure acceptable performance.
Automation can result in more consistent application of analysis methods and more timely results
Air filters
By trending the measured differential pressure across an air filter, it is possible to predict when filter replacement will be necessary (Figure 1). This will often result in lower costs compared to a conservative time-based filter-replacement schedule. If a particular filter is becoming loaded at a rate that significantly exceeds expectations, HVAC system component inspection or other maintenance activities can be scheduled. Other filters in pharmaceutical production equipment would also benefit from such analysis.
Redundant sensors
A bioreactor might have multiple redundant dissolved oxygen sensors in the same way that a steam sterilizer will have a monitoring and controlling sensor. A difference in readings between the two sensors that exceeds a given threshold for a specified period triggers an alarm. Trending the difference may reveal whether one sensor is drifting at an unacceptable rate; this would allow both sensors to be recalibrated before the next alarm occurs. Note that sensor recalibration due to trend analysis would generally be done in addition to recalibration at regular intervals.
Preventing excessive wear
Excessive wear caused by poorly tuned control loops or improper applications may cause valve and damper actuators to fail prematurely, even if the control loop or application was appropriate at installation and qualification. Utility pressure or temperature changes, for example, could result in excessive actuator movement; over the life of the actuator this can lead to wear. Calculation of accumulated actuator movement is straightforward using the time series of the actuator position, or using the time series of the position command signal if position feedback data are not available. If certain actuators are experiencing excessive movement, root cause analysis should be performed so that appropriate maintenance can be scheduled.
PredM in Aging Facilities
Facility operations staff should embrace PredM concepts by understanding facility and equipment performance, as well as risks to that performance. For aging facilities, PredM can play an important role in risk management and also contribute to the obvious potential for cost savings. Many attributes of an aging facility can be avoided through the correct implementation of PredM.
Most risks associated with aging facilities should be generally understood by facility personnel based on their operating experience. Ideally these risks have been documented (and periodically reviewed) as a part of a formal risk assessment process such as failure mode and effects analysis. Aging facilities often experience risks that recently commissioned facilities do not, such as the diminishing availability of spare parts for older equipment. Suppliers are valuable sources of information about aging equipment, and they may be able to provide specific recommendations about preventive maintenance and PredM procedures that will extend equipment life.
In some situations, more data will provide better predictive capability. Data in paper-based records, for example, can be entered into computer databases. Additional sensors may also be needed: While a mechanic might know that a gearbox should be inspected if it gets hot to the touch, for example, a sensor could monitor the gearbox temperature and generate an alarm when it exceeds a certain threshold. The mechanic’s knowledge is an example of tacit knowledge; adding an appropriate sensor and alarm can make that knowledge explicit. Of course, the cost and potential regulatory impact of such changes must be weighed against the expected benefits.
Given a good understanding of risks that may affect a facility’s ability to perform its missions and the costs of existing preventive maintenance programs, PredM can reduce risks and maintenance costs.