Innovations in Process Development and Manufacturing - Driving the Future of Pharma
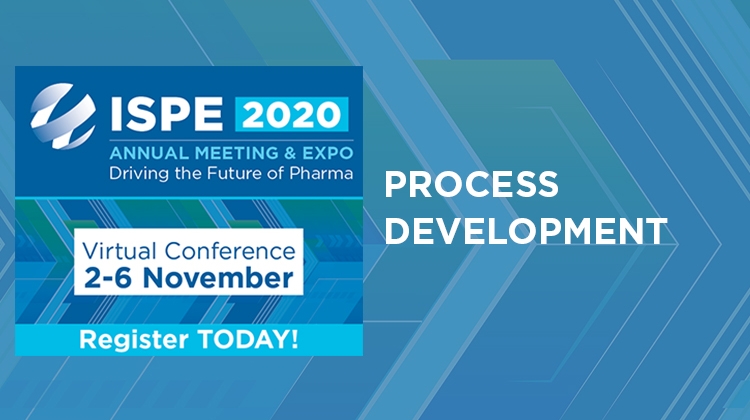
The needs of patients must always be at the forefront of what we do.
Many of our colleagues are taking on the challenge of rethinking the old ways. They are collaborating with each other and the regulatory agencies to take effective steps to remain at the forefront of regulatory science and innovation. Why? In order to ensure the continued delivery of effective medicines.
As we consider the future of pharmaceutical process development and manufacturing, we must identify the emerging needs of patients, assess the impact of these needs on manufacturing and process verification options, and work collaboratively to develop good practices. In addition, there is also a need to be intentional: to shape the knowledge management landscape and recognize the inherent culture changes required to be agile in today’s world. Especially with our “changed” world affected by the COVID-19 pandemic, this becomes even more important.
There are a number of emerging trends in pharmaceutical process development and manufacturing that will ensure that we can continue to deliver effective medicines to meet the needs of the patients. Moving into the future we need to consider faster speed-to-market, continuous and flexible manufacturing with an emphasis on knowledge management. The Process Development and Manufacturing Track cover these topics and more at all stages of the product lifecycle.
Key to development and scale up of drug products and active pharmaceutical ingredients (APIs) is defining process capability and robustness. Expert knowledge combined with predictive and prescriptive analytics will enable process understanding across a products lifecycle from lab-scale to commercial scale manufacturing. Leveraging this information will improve process robustness, process capability and the ability to manage risk. Gaining process understanding and knowledge management through the development of platform technologies, during process optimization and during technology transfer needs to be a priority as we move into the future.
An opportunity for smart and efficient manufacturing comes from the ability to utilize performance-based control strategies and advanced control strategies for controlling and optimizing a manufacturing process in real-time. Challenges associated with the application of these control strategies including how to develop, implement, validate and maintain need to be considered. This session will provide practical examples of performance based and advanced control strategies from different stages of the product lifecycle and lead to a discussion on opportunities for including automation and digitalization in line with Pharma 4.0 principles as well as the current challenges.
With companies having an increasingly diverse portfolio the need for facilities which can accommodate different process platforms is greater than ever before. For effective and efficient multi-product facilities, one needs to look at the number of different product types and how they might fit together. There are several factors to consider including product compatibility and synchronicity in shared resources. Focus will be given to multi-product ATMP facilities and ensuring a way to produce ATMPs quickly, efficiently and at appropriate scale. There are different commercial manufacturing strategies for cell based ATMPs that need to be considered as well (centralized, regionalized, point of care, outsourced). A panel discussion will provide insight into the impact of regulatory, supply chain, and process technology on the future vision of ATMP manufacturing.
Flexibility and modular manufacturing continue to be a developing trend for small batch, highly potent and high value drugs. This type of manufacturing leads to the need for flexible and modular equipment and even modular facilities. Examples of this type of manufacturing include a new flexible production cell and the development of a flexible state-of-the-art facility for high-potency manufacturing. In addition to commercial manufacturing modular facilities can accelerate product development which reducing development costs.
Following on from flexible and modular manufacturing, consideration will be given the manufacturing of high potent products in shared facilities. Content regarding how to design a facility and chose the right equipment for the manufacture of high potent substances will be covered. Consideration will be given to containment technologies and how they meet the required Permitted Daily Exposure (PDE) and Acceptable Daily Exposure (ADE), cleaning procedures and operator safety.
Check out the 2020 ISPE Annual Meeting & Expo Process Development and Manufacturing Track to see what we have in store. In addition, new registration rates have launched for this event making more affordable then ever to join your industry colleagues at the largest pharma event of the year.