Agility, Communication, & Strategy Are Key for COVID-19 Pandemic Response
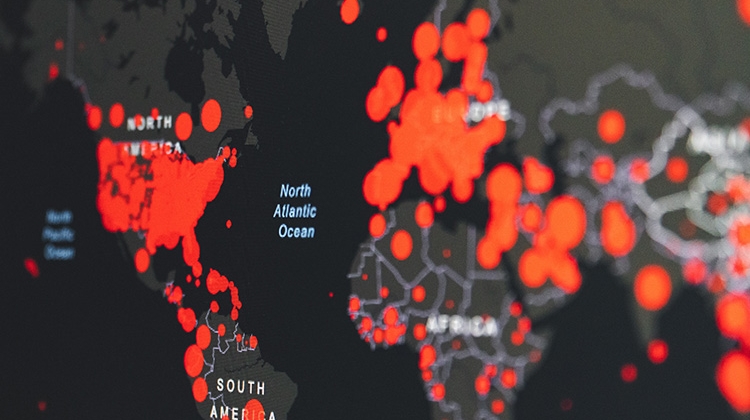
A panel of industry experts from a variety of disciplines discussed key challenges to the global pharma supply chain due to the current coronavirus pandemic during the “COVID-19: Pharma Supply Chain Security and Robustness During a Global Pandemic ” ISPE webinar on 2 April 2020. More than 660 attendees from 64 countries heard both strategies as well as predictions about future changes to the supply chain for pharma during the 60-minute webinar.
Although the industry is grappling with a situation that is constantly changing, the panelists identified trends that will help the industry weather the current storm and can lay the foundation for a more resilient and adaptable supply chain strategy after the pandemic.
Moderators

Panel Speakers




Davies opened the webinar by noting the focus of the discussion would be on supply of medicines globally during the uncertain times of the COVID-19 pandemic. “As we know, the manufacture and supply of pharmaceutical requires a truly global network, with manufacturing sites and supply chains stretching across countries and continents,” Davies said. “These supply chains are increasingly coming under strain as countries and individuals cope with the impact of COVID-19.” Affected areas include supplies of registered starting materials, APIs, excipients, consumables, packaging materials, drug product, finished goods, and PPEs with affects to date in countries including China, India, Italy, Spain, UK, and US.
He introduced the panel and each participant provided a short introduction about their role within their organizations as it pertains to supply chain, and then posed a series of questions to the panel. The questions were submitted by some of the more than 1,070 webinar registrants (not all registrants attended the live event but have access to the recorded webinar) as well as questions submitted during the course of the webinar.
Questions and Answers
Please expand on issues you are seeing today that are impacting the ability to supply products
Issues fall into three categories, said Ganguly, who is involved in supplier continuity, digital transformation for better remote work and operations, and procurement and fulfillment of supply chain at Gilead, a pharmaceutical manufacturer:
- The decentralized nature of the supply chain in the pharma industry has been better economically and for resilience, but getting that to simplified levels to assure service and supply is a problem now, he said. “The companies that are doing better with this are those that have invested in supply chain tools in the past,” Ganguly observed.
- Finding ways to technology-enable processes that were highly manual or done in person. “Doing FAT over Zoom with Google glasses is becoming par for the course,” he said. The situation has pushed a lot of organic innovation, Ganguly added. “Companies with a culture around breaking the status quo” are doing well with this.
- Working in an insular industry. There is an “unprecedented” amount of cooperation among regulators, suppliers, and localities. “This newfound collaboration is spurring innovation,” he said.
Morello, who leads supply chain planning and program management at Lonza, a CDMO, noted the impact of the supply chain and that working on the challenges presented is just beginning. He agreed with Ganguly about the great importance of communication, and added that the need for agility and flexibility in serving the CDMO customers are drivers now, as is daily activity to maintain connections with customers, including listening to the customer to make sure that the CDMO is doing what meets their needs.
Usinger, a leader in supply chain and customer project management at Vetter, a manufacturer and CDMO, noted the extremely rapid pace of change right now: change is happening day to day. He emphasized the importance of internal communication to get through this. CDMOs have an advantage here, he noted, because they are accustomed to adapting quickly and addressing challenges. “This is different for sure now, but our team is on board and looking forward to helping patients.”
What is the impact on supply, especially with clinical trial manufacturing development?
Morello noted that work on clinical trials is continuing since there is increased demand for new drugs to treat COVID-19. “We need to be flexible—it is a priority” to put available technology to use to address the need for COVID-19 drugs now.
Trone, who works on logistics, distribution, and transportation at UPS, the shipping/delivery company, noted that there are increased options for supplying products since many companies are stepping up to work with the FDA and CDC to get special permission to produce needed products that are not ones that they usually manufacture. “We’re working with them to get those products out into the market.” She noted the call to action from many state and federal agencies and well as individual manufacturers coming together to obtain product, primarily PPE and test kits, getting these sources, consolidating them into single locations, and pushing them out very quickly. “Speed and the ability to react immediately are the requests from the market,” she said.
What changes may be expected to the supply chain going forward?
Handfield, a professor of supply chain management whose work in this area has included pharmaceutical manufacturers and distribution companies and hospitals, noted that the current situation has exposed weaknesses around clinical trials and vaccines, PPE, API, and CDMOS, with over 24 countries restricting exports to other countries because of sourcing from remote locations. For instance, he said that 90% of masks are produced in China.
Outsourcing to low-cost countries results in the loss of a lot of flexibility, Handfield said. This was an issue during SARS. Right now, he sees a lot of activity but it is not well connected since entities are working on their own to get what they need to support their own providers, causing a lot of confusion in the marketplace.
Handfield predicted a return to localizing sources, calling it a “natural progression” from the current crisis situation. “People realize the need for local supply and manufacturing.”
What is actually happening in your facilities?
Ganguly spoke about best practices to keep facilities running when staff may be affected by the virus and the impact on morale. He said, “First, we talk about the fact that we have a patient mission, paralleled by the deep commitment to our workforce: their safety is our priority.” Gilead has identified critical operations not just for COVID-19 response but also those that ensure operations are kept compliant and safe, he said.
“There is a phenomenal amount of communication by all leadership levels down to shop leaders that we care deeply about their safety and their families’ safety.” Sending this message to employees and breaking down invisible barriers to make it clear that everyone in the facility is equally important has a very good impact on morale, Ganguly said.
In addition, Gilead is reexamining from a strategic viewpoint its 2020 goals “for what is truly essential: what to defer, delay, or outsource to other partners.” There is a retrospective approach as well: how to structure supply chains for more resilience in the future. “I expect the industry will tackle this once the dust settles.”
Morello said that the safety of Lonza’s people is paramount, including considerations about who should be onsite and who can work from home. Lonza is emphasizing regular communications each week on what is happening, with an emphasis on global commitment, and listening to what employees have to say on site about what management can do to help them to work and deliver.
Usinger said similar measures as those at Gilead and Lonza have been introduced at Vetter for employees, with a focus on communication. Employees have a lot of questions due to the fast changes and the information in the news, he said. An internal hotline was implemented for employees to respond to most questions and to explain steps that are being taken. The hotline has improved and professionalized the communications, he said.
How to ensure morale and safety for employees?
For UPS’s almost 500,000 employees, the company is equipping drivers with supplies and the understanding about safe deliveries, Trone said. Internal communications are important, and she noted they are a way to share interesting information about creativity and finding supplies that may not be available in the mainstream such as employees making masks by hand for staff or homemade hand sanitizer. “We’re proud of the stories internally that we are seeing,” she said. The focus is on 100% safety while trying to be there for the world in processing and delivering packages.
How does change control process allow for relatively quick changes in a highly regulated environment?
Usinger said that the supply challenges with masks and other protective clothing are bringing about impressive changes through looking at other sources and discussions with quality and production colleagues on how to implement these while staying within GMP regulations. “More collaboration and openness and willingness to consider other ideas and solutions to supply these critical materials” is bringing about faster change, he said. “It is nice to see what is possible when you collaborate together, that we can do this quite fast—and stick with GMP regs!”
At Lonza, Morello agreed, “GMP is not changing and we need to respect that.” The CDMO shows strength here in dealing with many different sources for different customers. This enables a quicker time to get approval for alternate sourcing.
Ganguly said the same approach is being taken at Gilead. “We’re not abandoning good fundamental change control policies,” he noted. What is happening is almost a more analytical approach to what is truly necessary for engineering, production, product safety, and compliance, he said. Understanding the critical attributes and impact to final products, and safeguarding those, ensures substitutability is evaluated. A lot of collaboration within departments and sites, with local agencies, cities, and regulatory bodies is part of this.
“Collaboration is really fundamental,” Handfield said. He noted that as all the panelists said, “in a crisis of this magnitude, you have to make do.” He added it is important to remember your suppliers: reaching out to make sure about their financial ability, working capital, and ability to get financing was really important. “If you are not in communication with those suppliers six months later, they may not be around.” Suppliers maintaining their health is important to the supply chain.
Is Just in Time dead?
“There is not a supply chain process that is dead,” Ganguly emphasized, noting the need for agility in supply chain considerations. “Supply chains heavily reliant on large inventory stock are now super resilient” rather than being seen as outdated. “Our ability to react to the next crisis will be less a function of a dominant supply chain model—it will be about agility, accepting change, and reacting appropriately. We will get over the crisis, and will go back to some of the Just in Time models for innovative therapies. We need to think about this question for the future.”
Handfield agreed that the next generation of supply chain will not be about less inventory, “but where do we keep it, and as Joydeep said, developing agile supply chains.” He observed that other industries such as automotive tend to use local suppliers for efficient communication and velocity of supply movement. How to drive greater collaboration, not just deciding on supply based on low price, and thinking about overall supply will be important. Rethinking stockpiles and business continuity as well as preparing for future events like COVID-19 will also be part of the future planning.
Panel Takeaways
The session wrapped up with each panel member sharing their takeaways from the group discussion of supply chain issues:
- Taking risk planning and management more seriously and have a healthy appreciation for these, even in times of no crisis. – Ganguly
- Risk management is becoming key and also pandemic risk management: are we really equipped for the risk we may face? This is a driver to a more efficient supply chain. – Morello
- Risk management: everyone is talking about it and I hope sustainability of supply chain with risk management will increase in future. Consider the cost of not having resources and capacities that are needed. – Usinger
- Continuity plans are a call to action to look at these in hindsight after COVID-19 to see if they made sense. Reflection will be significant activity we see after this is over. – Trone
- Understand the multistakeholder environment including employees, customers, and suppliers and the impact that this has had on all of them. Data and models are really critical now, and so is governance: central planning for supply and demand of critical materials to support healthcare and hospitals is needed in the US at least. We need more public and private sector collaboration with industry. In the next two weeks, we will need to come up with solutions for some very difficult times ahead. – Handfield
Didn’t get a chance to attend the COVID-19: Pharma Supply Chain Security and Robustness During a Global Pandemic webinar? Check out the ISPE Pharma Best Practices Webinar Past Recording page to listen to the recording now.