PPM uses machine learning algorithms to detect failure or anomaly patterns across equipment. These signatures correlate upstream process upsets, which means earlier failure prediction - up to weeks in advance - compared to traditional condition-based monitoring techniques. This allows more time to plan maintenance proactively or perform a preventative action, thereby avoiding potentially catastrophic failures. Moreover, prescriptive analytics enable the user to understand how a piece of equipment will fail, providing information on the most significant contributing factors. Overall, PPM democratizes access to machine learning, leveraging domain expertise and enabling subject matter experts to be proficient with artificial intelligence (AI) tools embedded in the technology.
PPM is a core component of Asset Performance Management (APM) as it holistically leverages data analytics, business goals and digital tools to improve the performance and reliability of assets and decrease maintenance costs. Figure 1 shows where PPM fits relative to system performance and quality assessment in an APM strategy.
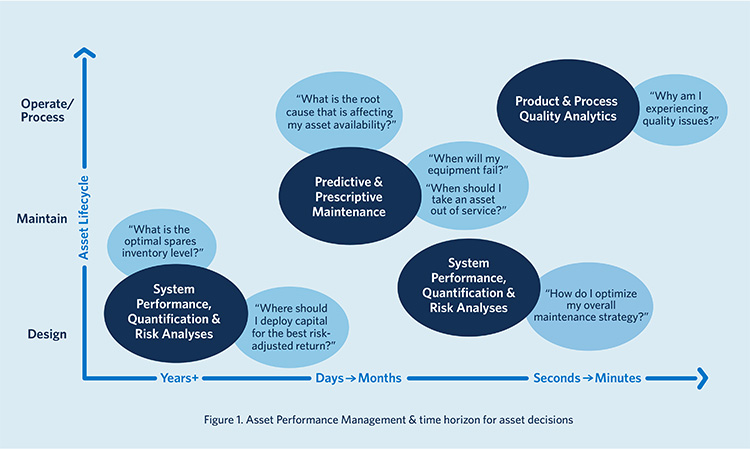
Leadership’s Role in Implementing Predictive and Prescriptive Maintenance
Leadership teams’ interest in PPM can be tied to initiatives for operational excellence (digital transformation and optimization of the asset lifecycle and asset reliability) and sustainability. In a recent report by AspenTech, in collaboration with FT Longitude, PPM was cited among the top four digital initiatives to improve operational agility and efficiency.
In the Verdantix Green Quadrant: Asset Performance Management Solutions 2022 Report
, 71% of the 256 respondents claim that implementation of asset management software to reduce maintenance-related costs is “very important.” Forty-eight percent of respondents stated that long-term digital initiatives that focus on environmental performance in line with government policies, environmental, social, and corporate governance (ESG) and carbon neutrality, are also of high priority. PPM supports this by early detection and mitigation of degrading equipment that improves efficiency on energy and materials, elimination of waste associated with failed batches, and avoidance of environmental incidents that can occur from catastrophic equipment failure.
Despite the obvious benefits, hesitations from leadership about implementing PPM in production facilities are still common. To be successful, it is imperative to establish governance and management sponsorship within the organization, as an interdisciplinary effort is required. An ideal governance structure would include operators and plant engineers, who would determine the best actions to take and the impact on equipment health; process engineers, who would analyze any process deviations; maintenance and reliability teams, who would monitor, predict, and mitigate asset issues; and business managers, who would assess risks and quantify business benefits.
Scalability as a Key Success Factor
Scalability across a site or multiple sites is a key success criterion for PPM deployment, and companies tend to evaluate this capability through a staged journey. Most often, the first phase is a pilot or proof of value over a 1-year period, where a target site or sites are chosen based on identified reliability issues, instrumentation availability, and alignment with internal digital initiatives. The scope is typically limited to critical equipment, and by the end of this initial phase, organizations have gained confidence, quantified the value based on predefined success criteria and integrated PPM into their daily operations.
The second phase is centred on expanding deployment to multiple sites, upskilling existing personnel, identifying and understanding key reliability initiatives, and aligning objectives at each site. In parallel, a continuous value capture process is conducted, based on the targeted business challenge and the associated asset within the production process. This serves as the business case framework and includes the targeted failure modes and anomalies that predictive maintenance will illuminate, and equally important, what actions should be taken after detection and the time that would require. The value capture process concludes with the quantification of business impact.
The most robust use cases for predictive maintenance deployments are typically associated with reoccurring losses, limited equipment availability, and process-based contributions to machine failure. These considerations are key differentiators of the value of PPM compared to traditional condition-based monitoring.
Predictive and Prescriptive Maintenance & Pharma 4.0™
PPM is an enabling digital technology within the ISPE Pharma 4.0™ framework and supports the FDA’s Advanced Manufacturing Initiative. An Axendia market research report
, which surveyed 199 life sciences professionals, showed that a combined 63% of life sciences companies have implemented, are piloting or plan to implement PPM initiatives within two years. The same research survey showed that PPM initiatives have a higher level of adoption by organizations who feel that advanced manufacturing is supported by existing regulatory frameworks.
Pharmaceutical companies are seeing the benefits of deploying PPM at multiple sites, such as monitoring and alerting on factors causing equipment degradation, optimizing equipment availability, and ensuring on-time delivery of medicines across product lines. A recent example
details how a large multinational pharmaceutical company ensured security of supply by implementing a PPM program that eventually rolled out to 30 sites. In one of the many applications implemented, PPM applied to a bead mill enabled seal replacement to be extended from every eighth to every twenty-fifth batch on average. The result was an estimated saving of $10,000 per seal. In addition, the greatest benefit came from increased production uptime due to the avoided maintenance, which delayed the need for capital investment into additional production capacity.
Despite pharmaceutical companies being at varying digital maturity levels, leadership teams are continuing to recognize how enabling technologies that break down data siloes are fundamental to furthering digital transformation across an enterprise. Implementing PPM programs help minimize production disruptions from equipment degradation and can gain millions of dollars in saved batches and increased uptime, improve consistent on-time delivery of high-quality medicines, and deliver on the collective responsibility in achieving global sustainability goals.
To learn more, join ISPE on 6 December for the complimentary webinar Making Maintenance a True Asset in Pharma Manufacturing Through Digitalization. Sponsored by AspenTech, this webinar will explore new opportunities created by a digital APM strategy.
Register Now
iSpeak Blog posts provide an opportunity for the dissemination of ideas and opinions on topics impacting the pharmaceutical industry. Ideas and opinions expressed in iSpeak Blog posts are those of the author(s) and publication thereof does not imply endorsement by ISPE.