Treating Spare Parts Storeroom as Critical Quality System & Strategic Company Advantage
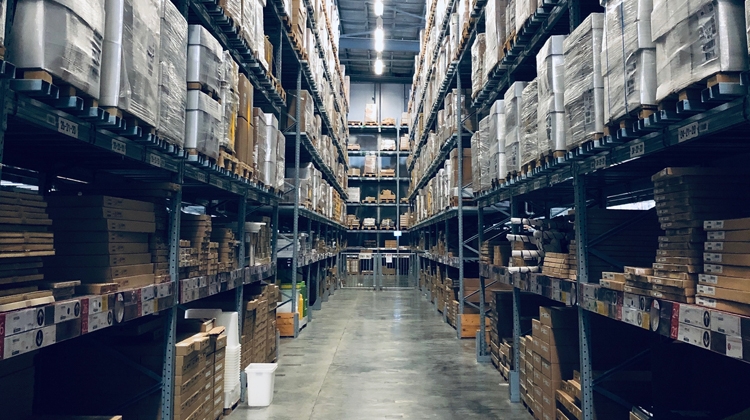
In too many cases, the Spare Parts Storeroom has become the unavoidable appendage to the functioning of the Maintenance and Facilities Departments. The importance and support it should receive constantly fail to reach acceptable levels. In many other industries, this will mean either a lack of management or an increase in bad practices. But in the Life Sciences sector, this situation will eventually lead to a state of non-compliance, gross over-spending, or excessive downtime and lost production/research.
This discussion is intended to highlight how a Spare Parts Storeroom can be approached as a critical quality system element and be treated as a strategic company advantage.
Just like safety, in our industry Quality must always be our primary concern. It is not surprising, therefore, that we should look at the way equipment parts are set up, procured, issued, received, and stored.
Firstly, the setting up of new spares. Only fully vetted, qualified distributors and OEM vendors should be the primary suppliers of spare parts. The relationship between customer and vendors should be one of trust and open communications. This will typically begin at the purchase of new equipment, where the recommended spare parts lists will be evaluated, and the local suppliers identified. The procuring Engineer, Purchasing and the Storeroom Manager, will conclude as to the range and volume of parts required to maintain this equipment in its’ validated state. The Storeroom Manager then will request or create the appropriate CMMS (computer maintenance management system) inventory records. It may be the company policy at this time to indicate certain unique qualities of these parts, e.g. repairable, product contact, GXP, Insp req’d, etc. Following this, it will be the responsibility of Maintenance to ensure that this information, i.e. inventory records, are linked to equipment through the BOM functionality. The BOM, therefore, becomes the official record of spare parts required for the maintenance of equipment used in the production of drug products under the purview of regulatory agencies.
Next will come the act of procurement. In order to retain the most optimal levels of inventory, an efficient and clear process must be employed, to provide fast replenishment of parts while keeping order points as low as possible. Suppliers have to be constantly aware that substitutions of any kind are not acceptable without the appropriate review and approval. Purchase Orders must have clear instructions indicating these conditions. Even, and most importantly, when this comes to materials of construction. In cases where the part manufacturer has changed to a different material, it should be stressed with all people downstream, that this event has occurred. Incidents like this have happened, with the effect of causing investigations and product recalls.
Accurate reordering is reliant upon accurate issues. An open Storeroom, where technicians retrieve their own parts, can make accuracy in issuing a challenge. Charging out the parts to the wrong equipment will create a misunderstanding of the equipment’s needs, charging out the wrong item number creates multiple problems. First the inventory is off on the item taken, secondly, an item is reordered when it was not required. Regulatory agencies are not, in principle, concerned with inventory accuracy (it may be considered, however, as a lack of control), but they are attentive to reverse traceability. If an instrument was calibrated using a consumable standard in inventory, then the details, e.g. lot number, expiration date, etc. are critical quality elements. Anyone who has had to conduct investigations regarding use and installation parts, will be familiar with the effort to ascertain if the correct item has been installed in the equipment in question.
Receiving and inspection procedures are necessary for the consistent and standardized methods to onboard parts correctly. This is the first chance to discover where mistakes may have been made. The person conducting this act should be the one responsible for managing the inventory. If the receiving is done at another location and by another department, then errors will slip through and sometimes may not become detected. Most CMMS systems have the functionality to accommodate a second check inspection. This can be configured with an e-sig and audit trail report.
All the previously mentioned processes must be covered under detailed and comprehensive SOP’s. These instructions will form the foundation of practices and procedures to be followed to operate this Life Sciences Spare Parts Storeroom in a consistent and compliant manner.
Setting up a GXP compliant Spare Parts Storeroom is an investment that will pay out every time an inspection is scheduled. A clean, well laid out, organized facility will provide the assurance to an Investigator that this inventory is under tight control and follows established standard processes. The recommendation to put all parts possible into plastic closable bags has a number of benefits:
- It keeps the item in a clean state
- The item number can be written on the bag, not the part
- Helps with inventory counting
- Facilitates barcoding
Keeping parts clean and unmarked facilitates any returns of overstocks, or unneeded/obsolete spares. A logical and easy to read location scheme, along with clear bin/shelf labeling, significantly reduces picking errors.
Treating the Spare Parts Storeroom as a critical Quality System Element, like many other processes involved with the manufacture of drug products, will ensure that procedures will be followed, and that the operation will function more efficiently and effectively. Many other more granular aspects of this endeavor will become apparent, but the first step is looking at the Storeroom anew and mapping out current state to future state paths.
Another facet of the Spare Parts Storeroom is the significant investment it holds, as well as the impact it can have on the overall efficiency of Maintenance. The following dialogue will shed light on how this operation can benefit an organization through the implementation of some well-established, comprehensive practices. The strategy will focus on two elements, reducing inventory to optimal levels, and providing value-added services to its’ major customer, Maintenance.
The common accounting formula is that inventory like spare parts will have a total holding cost of between 15-20% of the cost of inventory value. This may be calculated by the on-hand quantity multiplied by a unit cost. This can be one of three cost values, initial (or standard) cost, last price paid, or average price. Each has nuances and will be selected according to your company policies. By a judicial and careful examination of the inventory levels and costs, a person can change that figure and by doing so reduce the overhead cost for the Corporation.
So, if we can establish a data point of Inventory Value, we can then assign a cost of holding for that population of parts. That will become part of the formula for an aggressive inventory optimization process. Using an example of an Inventory Value of $10,000,000 then the holding cost would be $150,000 – $200,000. This figure will include a multitude of elements like payroll, utilities, the cost of capital, etc.
Therefore, treating the inventory as a strategic advantage, a company will be trying to reduce that inventory value, and coincidently reducing the holding costs.
This will be done through many different methods- removing excess inventories, cleaning up obsolete parts, and a careful review of inventory levels.
In order to bring down inventory levels, a new relationship with some suppliers may need to be established. It has become a common trend for suppliers, vendors, distributors to attempt to push the holding of inventory down to the customer. This is not an acceptable practice. The very term “Distributor” should indicate that this is part of the supply chain. It is the responsibility of the supplier to act as their name implies. This fact should be part of the equipment selection process, listed under sustainability. When making large equipment decisions, the after-care including the ability to obtain spare parts expeditiously must be part of that consideration.
The aggressive approach to removing obsolete inventory is one that is rarely completed. A lack of understanding the historical demand patterns is one of the factors preventing inventory managers from discarding parts. Without accurate, timely, and consistent data, the program to remove spares will fall into the realm of using “tribal knowledge” about what is needed and what is not. When this occurs, another quality enters the equation, and that is emotional attachment. Too many times you will hear the maintenance person, with many years’ experience, insist on retaining parts, because they have helped them out of a “jam” in years past.
Excess inventory is a result of many actions: from a “return to stores” effort to clean up the plant, as leftover materials from capital projects, from the closing of sister plants with similar inventories. No matter where the stream comes from, the basic response must be:
- Will we consume these items in a timely manner (one to five years)?
- Is it for equipment that is currently installed at this location?
- Are the parts in pristine (resalable) condition?
In order to approach this methodically, the first step is to control the influx. With the return to stores effort, set ground rules demanding to indicate the use of parts. As for the leftover project materials, the project engineer should be made responsible for the cost recovery of capital parts. Finally, with incoming spares from sister plants, the management must be aware that free is not really free. As mentioned before, holding costs can be significantly increased through the adoption of this material.
There are many other ways that a well-run, optimized, and coordinated GXP Storeroom can add value to the Maintenance operation. By employing the idea that it is more efficient for the parts to go to the work areas, than the mechanics to come for the parts, is one very important factor. This enhances the planning and scheduling efforts and will dramatically increase the potential wrench time available. One person making deliveries of parts kits will effectively increase efficiencies of the maintenance mechanics. So much productive time is wasted by employees searching the storeroom for parts to complete their jobs.
Another facet is the keeping of inventory accuracy at a world-class level i.e + 98%. When there are levels below this value, a substantial impact on planning and scheduling will be felt. If a stated accuracy of, say 70% has been reported, then it is not outside the realm of possibility that 3 out of 10 requests for parts will go unfulfilled. On a weekly schedule, this may just mean moving to other work, but in some cases, it may mean that critical equipment may not be able to be restarted. If these assets are part of major production runs, or integral to on-going research, then the effect can be dramatic.
So, in conclusion, the GXP Storeroom has the potential to be a definitive, measurable and competitive advantage that is completely within the control of the site operations. It only takes the people concerned with executing repairs, projects, and PM work, to view the GXP Storeroom as a positive and collaborative tool for increasing the competitive edge.